Catalogo Family 05 - codice 0440 - Vedi tutti i dettagli:
Pagina 1
1. BIOGRAFIA FAMILY 05
2. FAMILY 05
Pagina 2
3. CICLI DI FUNZIONAMENTO
4. RICARICA ESTINTORI A POLVERE ABC-BC
5. COLLAUDO IDRICO
6. PANNELLO DEI COMANDI ELETTRICI
7. PANNELLO DEI COMANDI E DELLE DERIVAZIONI DI IMPIANTO
8. EMERGENZA E SICUREZZA
Emme Antincendio srl è lieta di presentare il suo nuovo VIDEO CATALOGO del macchinario FAMILY 05 ! Cosa significa video – catalogo ? Significa un catalogo che è possibile leggere normalmente come ogni altro catalogo a differenza che in gran parte dei suoi argomenti ha anche una sessione video tutta da vedere per chi ha meno voglia di leggere.
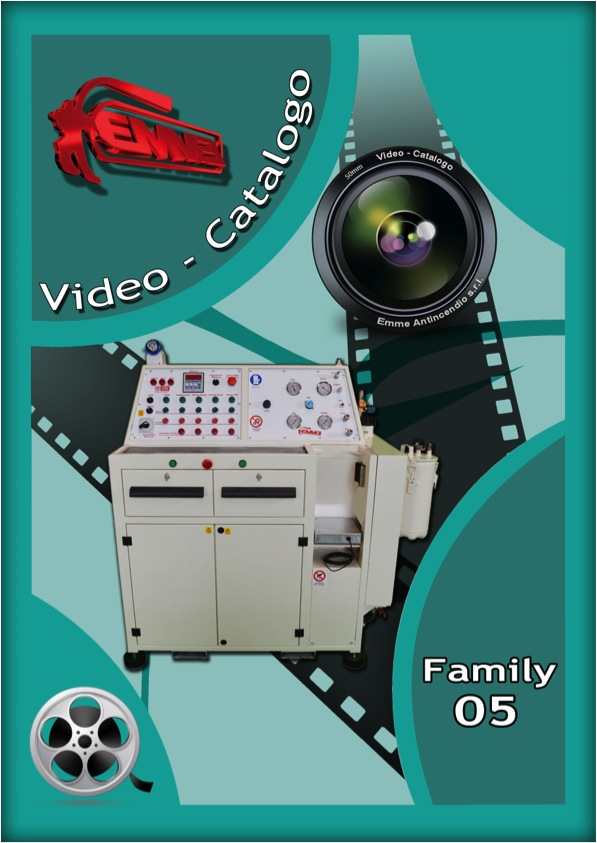
Prima di procedere alla lettura del catalogo Vi preghiamo di leggere alcune semplici “istruzioni”.
Troverete dei simboli all’interno , qui di seguito vediamo il loro significato..
Ogni volta che troverete questo simbolo significa che ci sono degli approfondimenti curiosi da leggere.
Ogni volta che troverete questo simbolo, è sufficiente cliccarci sopra e potrete avere il video della sessione relativa, così potrete scegliere se leggere oppure guardare ed ascoltare
Ogni volta che troverete questo simbolo significa che seguiranno le procedure d’uso relative ad un certo dispositivo o ad un certo processo di lavoro
Ogni volta che troverete questo simbolo significa che ci sono delle foto su dei particolari importanti
BIOGRAFIA
Dall’entrata in vigore della normativa UNI9994 del 1992 la Emme antincendio si è sempre distinta per un servizio di alta qualità e da sempre ha cercato di perfezionare il rapporto con i clienti cercando soluzioni e novità sempre al passo con i continui cambiamenti del mercato. Nel 1998 nacque l’idea della Family 05 , in quel momento non esisteva un’attrezzatura in commercio che permettesse ai manutentori di fare le dovute operazioni sugli estintori nel rispetto della normativa con dei macchinari specifici e soprattutto era impossibile effettuare certi tipi di controllo sul posto , cioè direttamente dal cliente. Le apparecchiature esistenti erano tutte molto ingombranti e di svariato genere.
Fu per questo motivo che Gian Franco Milli creò una macchina in grado di essere installata direttamente nei furgoni dei manutentori ed in grado di poter effettuare qualsiasi tipo di controllo come richiedeva la normativa, che andasse a sostituire tutte le apparecchiature allora in commercio, una macchina all-inclusive con la quale poter fare anche il servizio a domicilio.
Ma l’idea non si limitava al solo controllo ed al collaudo idrico di estintori a polvere , co2, gas e schiuma, ma anche al riavvolgimento ,al controllo ed al collaudo idrico ed a secco delle manichette antincendio UNI 25-45-70. Quindi una macchina completa ed unica nel suo genere che avrebbe rivoluzionato il mondo delle manutenzioni.
Un primo prototipo fu progettato , realizzato e brevettato nel 1998 , la macchina si presentava già molto compatta e già in grado di effettuare molte operazioni in maniera semplice , ma dopo qualche anno furono apportate delle migliorie sia dal punto di vista meccanico che estetico , fino ad arrivare alla versione definitiva nel 2009.
La Family 05 non è stata più cambiata fino a poco tempo fa, si tratta però di un restyling di carpenteria e quindi esclusivamente estetico che ha reso la macchina più gradevole nel suo aspetto .
La Family 05 è un macchinario molto compatto che può essere installato anche in azienda ma che si presta benissimo per essere installata nei classici furgoni usati dai manutentori e anche su mezzi più piccoli, grazie alle sue dimensioni molto ridotte ed alla sua carpenteria robusta. Con la versatilità e la varietà delle sue funzioni permette agli utilizzatori un forte abbassamento dei costi ed un aumento dell’efficienza del servizio, racchiude infatti le capacità operative di 8 macchinari di vecchia concezione e abbassa notevolmente il tipo di investimento per le aziende di manutenzione.
Ma perché il nome FAMILY05 !?
Il nome viene da 2 motivi ,il primo è che la famiglia Milli è composta da 5 persone Gian Franco, Adriana, Barbara, Marco, Alberto … e quindi per esprimere tutta l’energia possibile di 5 persone. Il secondo è che nella Family05 ci sono 5 elementi fondamentali che sono la pompa a vuoto, la pompa idrica, pompa per travaso del CO2 in fase liquida, il compressore ad aria e la bilancia elettronica con morsa pneumatica.
DATI TECNICI
La macchina è contraddistinta dalle diciture punzonate sulla targhetta metallica applicata sulla parte laterale del telaio.
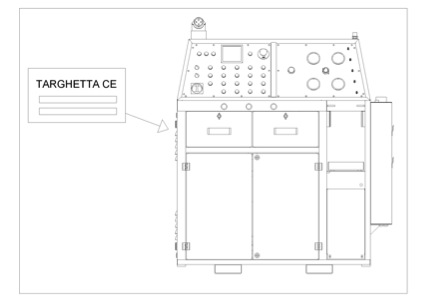
DESCRIZIONE DICITURE PUNZONATE SULLA TARGHETTA MECCANICA
|
MODELLO
|
Modello macchina
|
No. SERIE
|
Numero serie
|
TIPO
|
Tipo di macchina
|
ANNO
|
Anno di fabbricazione
|
MASSA
|
Peso macchina in Kg
|
POTENZA
|
Potenza macchina in kW
|
ALIMENTAZIONE
|
Tensione di alimentazione
|
VOLT
|
Tensione di alimentazione
|
AMPERE
|
Corrente elettrica
|
La macchina è contraddistinta anche da una targhetta che riporta le caratteristiche elettriche del quadro di potenza. La targhetta in questione è posizionata all’interno del quadro elettrico.
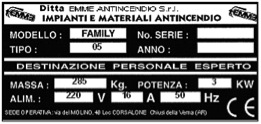
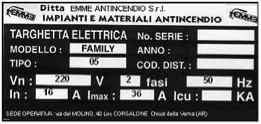
DESCRIZIONE DICITURE PUNZONATE SULLA TARGHETTA ELETTRICA
|
Fornitore
|
Codice di riferimento della macchina
|
Nr. serie
|
Numero di serie
|
Un
|
Tensione nominale e numero delle fasi
|
f
|
Frequenza elettrica in Hz
|
In
|
Corrente a pieno carico
|
II max
|
Corrente nominale del carico maggiore
|
Icu
|
Potere di interruzione di corto circuito
|
Codice Distinta
|
Codice distinta componenti elettrici
|
Anno
|
Anno di costruzione della centralina elettrica
|
FAMILY 05
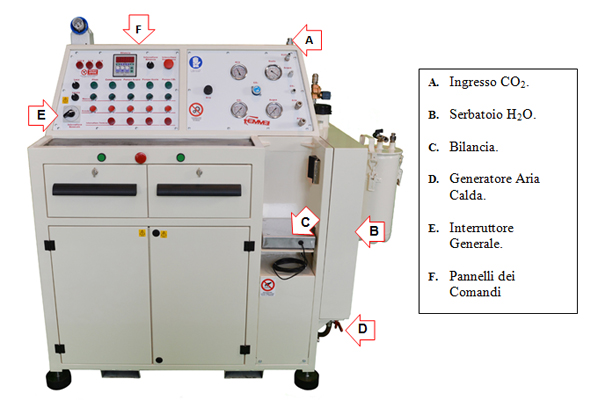
Il principio di funzionamento della macchina si basa su una serie di interventi da effettuare su diversi tipi di estintori. Per effettuare questi interventi sono stati assemblati, in un unico impianto, alcuni gruppi operatori ognuno con una mansione specifica.
Tutti i gruppi operatori fanno capo ad un controllo che gestisce le diverse fasi operative della macchina.
Le regolazioni e la messa a punto dei vari gruppi operatori sono gestite dal quadro elettrico tramite un PLC, che permette di predisporre la macchina adeguatamente alle varie mansioni da svolgere su di ogni estintore.
La FAMILY 05 è una macchina progettata e realizzata per effettuare il controllo ed il collaudo degli estintori rispettando le prescrizioni previste dalla normativa UNI 9994-92 *.
La macchina permette le seguenti operazioni:
Ricarica estintori a CO2 e a Gas:
-
utilizzo di una pompa a pistoni per il travaso dell'agente estinguente liquido ad alta o bassa pressione (da serbatoio a serbatoio e da tank di stoccaggio a serbatoio).
Ricarica estintori a polvere ABC:
-
utilizzo di una pompa a vuoto, corredata di filtri di protezione, per il travaso delle polveri in operazioni di caricamento e svuotamento (quest'ultimo prevede l'ausilio di un contenitore apposito).
Collaudo idrico:
-
attraverso l'impiego dell'acqua si verifica la stabilità del serbatoio dell'estintore con una prova idrica della durata di 30 secondi ad un valore massimo di pressione punzonato sul sebatoio stesso; è possibile, su richiesta, collaudare anche estintori a CO2 dove è necessaria una pressione di 250 Bar.
* Estratti informativi dalla norma UNI 9994-1 : 2013
Scopo e campo di applicazione
La presente norma prescrive i criteri per effettuare il controllo iniziale , la sorveglianza, il controllo periodico , la revisione programmata ed il collaudo degli estintori di incendio , ai fini di garantirne l’efficienza operativa. La norma si applica alla manutenzione ordinaria e straordinaria degli estintori di incendio portatili e carrellati , inclusi gli estintori d’incendio per fuochi di classe D. La normativa non si applica alle attività di installazione degli estintori di incendio.
Riferimenti
UNI 8633 Manometri ,vacuometri e manovacuometri con elemento elastico a molla Prescrizioni tecniche di collaudo e di accettazione
UNI 9492 Estintori carrellati d’incendio - Requisiti di costruzione e tecniche di prova
UNI EN 341 Lotta contro l’incendio ,Estintori d’incendio portatili
Designazione durata di funzionamento prova di efficacia
UNI EN 342 Lotta contro l’incendio ,Estintori d’incendio portatili (tenuta, prova dielettrica, prova di costipamento, disposizioni speciali)
D.P.R nr. 524 8 Giugno 1982: Attuazione della Direttiva nr. 77/576/CEE per il ravvicinamento delle disposizioni legislative, regolamentari ed amministrative degli Stati Membri in materia di segnaletica di sicurezza sul posto di lavoro e della Direttiva nr. 79/640/CEE che modifica gli allegati della direttiva suddetta.
Terminologia
Ai fini della presente norma si applicano le definizioni seguenti:
4. Estintore: apparecchio contenente un agente estinguente che può essere proiettato e diretto su un fuoco sotto l’azione di una pressione interna. Questa pressione può essere fornita da una compressione preliminare permanente, da una reazione chimica o dalla liberazione di un gas ausiliario (definizione conforme a UNI 9492 e UNI EN 3/1)
5. gas ausiliario (definizione conforme a UNI 9492 e UNI EN 3/1)
6. Estintore portatile: estintore concepito per essere portato e utilizzato a mano e che, pronto all’uso , ha una massa minore o uguale a 20 kg (definizione conforme a UNI EN 3/1)
7. Estintore carrellato: estintore trasportato su ruote, di massa totale maggiore di 20 kg e contenuto di estinguente fino a 150 kg (definizione conforme a UNI 9492)
8. Agente estinguente: complesso del o dei prodotti contenuti nell’estintore la cui azione provoca l’estinzione (definizione conforme a UNI 9492 e UNI EN 3/1)
9. Carica di un estintore: massa o volume dell’agente estinguente contenuto nell’estintore. Dal punto di vista quantitativo, la carica degli apparecchi a base d’acqua si esprime in volume (litri) e quella degli altri apparecchi in massa (chilogrammi), definizione conforme a UNI EN 3/1.
10. Omologazione (approvazione di tipo) procedura tecnico - amministrativa con la quale viene provato il prototipo di estintore, certificata la rispondenza alla norma ed emesso da parte delle Autorità Competenti il provvedimento di autorizzazione alla riproduzione del prototipo stesso, prima della immissione sul mercato.
11. Produttore: chiunque fabbrichi, assembli ed immetta sul mercato l’estintore completo delle sue parti e pronto all’impiego.
12. Manutentore: persona fisica o giuridica specializzata e autorizzata all’espletamento del servizio di manutenzione degli estintori.
13. Cartellino di manutenzione: documento che attesta gli interventi effettuati in conformità alla presente norma.
Classificazione
In relazione all’agente estinguente gli estintori si suddividono in:
13. estintori ad acqua;
14. estintori a schiuma;
15. estintori a polvere;
16. estintori ad anidride carbonica (CO2);
17. estintori ad idrocarburi alogenati.
Di seguito un estratto della nuova normativa UNI9994-1:2013 sulle fasi di manutenzione degli estintori :
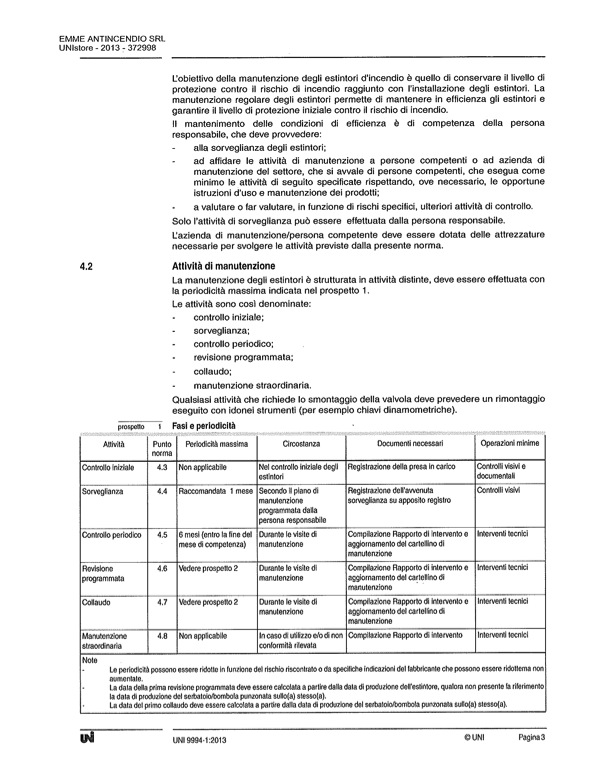
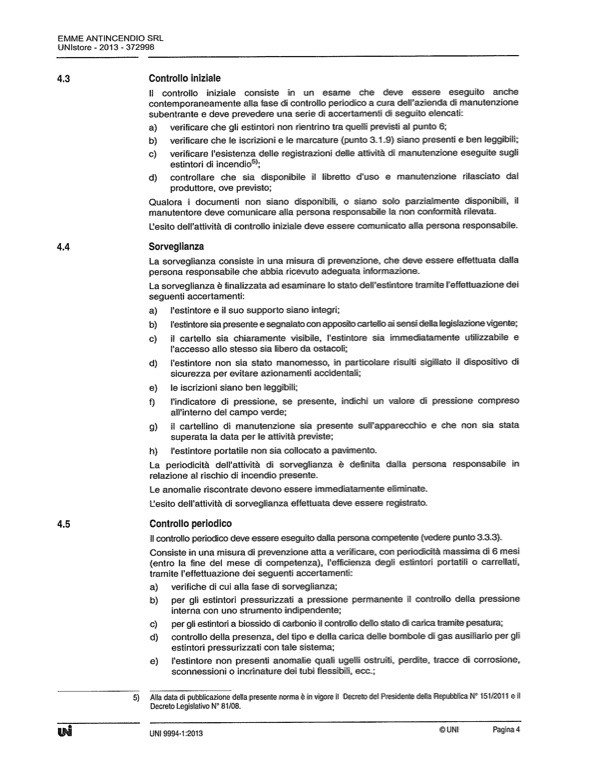
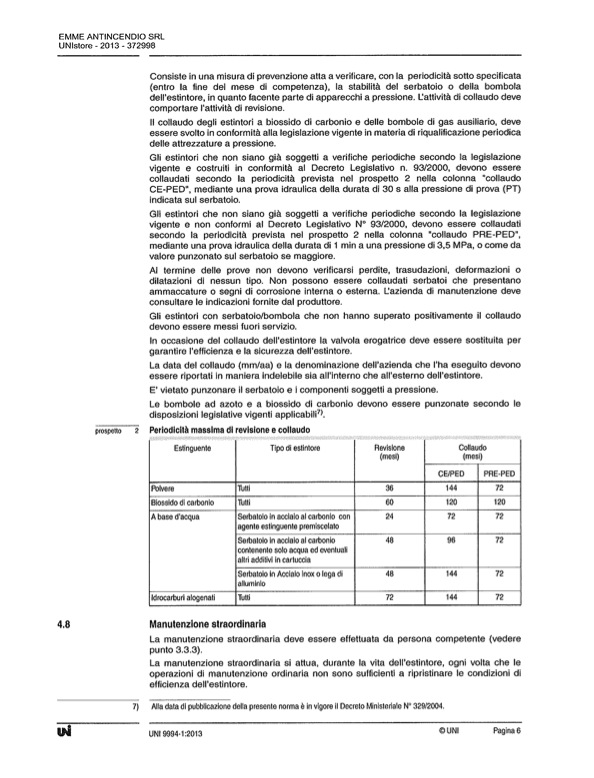
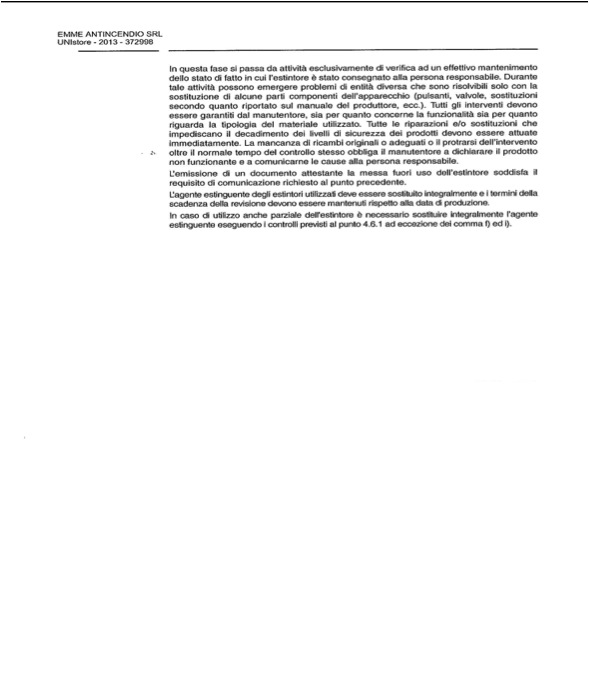
DATI TECNICI
|
MODELLO
|
FAMILY 05
|
Dimensioni d’ingombro totali (LxPxH)
|
1212 mm x 580 mm x 1320 mm
|
Dimensioni del piano di lavoro (LxP)
|
840 mm x 227 mm
|
Altezza del piano di lavoro (H)
|
977 mm
|
Corsa massima del sistema di bloccaggio pneumatico
|
200 mm
|
Peso (massa totale)
|
Circa 280 kg.
|
Alimentazione
|
220 Vca - 50/60 Hz - 16A
|
Potenza assorbita
|
Massimo 3 KVA
|
Livello massimo di rumore
|
70 dB
|
Velocità massima di riempimento
|
Polvere
3 kg/min.
|
Anidride carbonica (CO2)
2,5 kg/min.
|
Velocità di collaudo
|
Circa 1,5 min. per raggiungere 3,5 Mpa
|
Elenco norme relative alla sicurezza della macchina
La macchina è stata realizzata conformemente alle norme di sicurezza sottoelencate in quanto si ritiene rappresentino, come risultato dei lavori in ambito delle commissioni CEN, il più elevato livello in materia di sicurezza.
- Direttiva 98/37/CE Nota come “Direttiva Sicurezza Macchine”
- Direttiva 2006/95/CE Bassa Tensione (DBT)
- Direttiva 89/336/CEE Relativa alla Compatibilità Elettromagnetica (EMC)
- Direttiva 93/68/CEE Modifica la direttiva 89/336/CEE relativa alla marcatura CE
- EN 12100-1 Sicurezza del macchinario – Concetti fondamentali, principi generali di progettazione. Parte I: Terminologia, metodologia di base.
- EN 12100-2 Sicurezza del macchinario – Concetti fondamentali, principi generali di progettazione.
- Parte 2: Specifiche e principi tecnici.
- EN 294 Sicurezza del macchinario – Distanze di sicurezza per impedire il raggiungimento di zone pericolose con gli arti superiori.
- EN 349 Sicurezza del macchinario - Aperture minime per evitare lo schiacciamento di parti del corpo umano.
- EN 414 Sicurezza del macchinario – Regole per la stesura e la redazione di norme di sicurezza.
- EN 418 Sicurezza del macchinario – Impanto di arresto di emergenza, aspetti funzionali. Principi di progettazione.
- EN 626-1 Sicurezza del macchinario – Riduzione dei rischi per la salute risultanti dall’emissione di sostanze pericolose emesse dalle macchine.
Parte 1 – Principi e specifiche per i costruttori di macchine.
- EN 626-2 Sicurezza del macchinario – Riduzione dei rischi per la salute risultanti dall’emissione di sostanze pericolose emesse dalle macchine.
Parte 2 – Metodologia che porta alle procedure di verifica.
- EN 953 Sicurezza del macchinario – Requisiti generali di progettazione e costruzione dei ripari: Ripari fissi e mobili.
- EN 981 Sicurezza del macchinario – Sistemi di segnali di pericolo e di informazione uditivi e visivi.
- EN 1037 Sicurezza del macchinario – Isolamento e dispersione di energia – Prevenzione di avviamenti inaspettati.
- EN 1050 Sicurezza del macchinario – Principi per la valutazione del rischio.
- EN 1088 Sicurezza del macchinario – Dispositivi di interblocco associati ai ripari. Principi di progettazione e di scelta.
- EN 9432 Acustica. Determinazione del livello di esposizione personale al rumore nell’ambiente di lavoro.
- EN 11200 Acustica. Rumore emesso dalle macchine e dalle apparecchiature. Linee guida per l’uso delle norme di base per la determinazione dei livelli di pressione sonora al posto di lavoro e in altre specifiche posizioni.
- EN 11202 Acustica. Rumore emesso dalle macchine e dalle apparecchiature. Misurazione dei livelli di pressione sonora al posto di lavoro e in altre specifiche posizioni. Metodo di controllo in alto.
- EN 60204-1 Sicurezza del macchinario - Equipaggiamento elettrico delle macchine
Parte 1: Requisiti generali
- EN 60439-1 Apparecchiature di protezione e di manovra per bassa tensione (quadri BT)
Parte 1: apparecchiature soggette a prove di tipo (AS) a apparecchiature parzialmente soggette a prove di tipo (ANS).
- EN 60529 Gradi di protezione degli involucri (Codice IP).
- EN 60947-4-1 Interruttori e comandi a bassa tensione.
Parte 4: Contattori elettromeccanici e avviatori per motori.
- EN 60947-5-1 Interruttori e comandi a bassa tensione.
Parte 5: Dispositivi dei circuiti di comando ed elementi di commutazione.
Parte 1: Dispositivi elettromeccanici dei circuiti di comando.
- UNI EN ISO 13849-1 Sicurezza del macchinario – Parti dei sistemi di comando legate alla sicurezza.
Parte 1: Principi generali per la progettazione.
- EN 983 Sicurezza del macchinario – Requisiti di sicurezza relativi a sistemi e loro componenti per trasmissioni oleoidrauliche e pneumatiche. Pneumatica
Zone pericolose
La macchina non presenta zone in cui l’operatore corre grandi rischi di infortunio.
Con riferimento alla figura (Fig.3.1), le zone pericolose opportunamente protette dai dispositivi di sicurezza, sono elencate e localizzate:
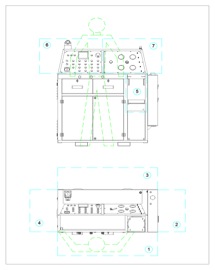
Fig. 3
-
Zona anteriore (Fig.3-1) relativamente alla fase di carico e scarico dell’involucro o dell’estintore nel vano di bloccaggio pneumatico: pericolo di schiacciamento, cesoiamento, caduta dell’oggetto da caricare (involucro o estintore), caduta del materiale da trasferire (polveri o acqua), pericoli.
-
Zona laterale destra (Fig.3-2) relativamente alla fase di carico e scarico dell’oggetto da caricare nel vano di bloccaggio pneumatico: pericolo di schiacciamento, cesoiamento, getti di aria calda dal ventilatore industriale posto in basso.
-
Zona posteriore (Fig.3-3) relativamente alle eventuali attività di manutenzione e di regolazione dei gruppi operatori localizzati all’interno del vano macchina: pericolo di cesoiamento, impigliamento, getti a pressione medio-elevata di fluidi.
-
Zona laterale sinistra (Fig.3-4) relativamente alle eventuali attività di manutenzione e di regolazione dei gruppi operatori localizzati all’interno del vano macchina: pericolo di cesoiamento, impigliamento, getti a pressione medio-elevata dei fluidi dei vari circuiti.
-
Zona vano carico e scarico (Fig.3-5) dell’involucro o dell’estintore da trattare: pericolo di schiacciamento, cesoiamento, caduta dell’involucro o dell’estintore da trattare.
-
Zona quadro elettrico di controllo e consolle di comando (Fig.3-6): pericolo di contatto con parti in tensione.
-
Zona controllo della pressione e attacchi rapidi (Fig.3-7): tubi in pressione.
Dispositivi di sicurezza
La macchina risponde a tutti i requisiti di sicurezza imposti dalla Direttiva Macchine relativi ai principi di integrazione della sicurezza attiva.
In riferimento alla figura (Fig.4), le misure di prevenzione del rischio di infortuni sono state attuate nelle varie zone della macchina.
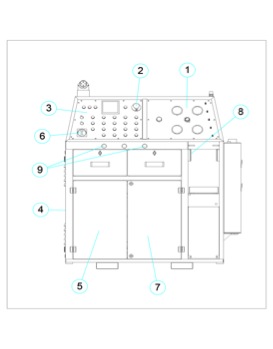
Fig. 4
-
Comando a due mani (Fig.4-9) per l’attivazione del bloccaggio dell’involucro o dell’estintore nel vano di trattamento: l’operatore, dopo aver collocato l’oggetto da trattare nel vano di bloccaggio pneumatico, aziona contemporaneamente i due pulsanti di comando a due mani. La morsa pneumatica (Fig.4-8), blocca l’oggetto da trattare tenendo impegnato l’operatore in una zona non pericolosa per lo schiacciamento o il cesoiamento.
-
Ripari laterali mobili (lato sinistro): disposti a protezione dell’accesso laterale dalle parti mobili ed interbloccate con microinterruttore di sicurezza; la rimozione dei ripari, è possibile solo con atto volontario che causa l’arresto della macchina. (Fig.4-4).
-
Ripari anteriori mobili: disposti a protezione dell’accesso anteriore alle parti in movimento ed interbloccate con microinterruttore di sicurezza. L’accesso all’interno del vano, dove sono riposti i gruppi operatori, è reso sicuro dalla totale assenza di energia elettrica e perciò dall’impossibilità di avere parti in movimento. (Fig.4-5,7).
-
Ripari fissi di parti in movimento: ulteriori ripari fissi, sono stati messi su organi in movimento (pulegge, ingranaggi, cinghie in movimento, ecc.) posti all’interno del vano dei gruppi operatori
-
Ripari fissi posteriori: disposti a protezione del vano dei gruppi operatori in modo da evitare intromissioni con organi in moto. La protezione è realizzata in lamiera di spessore adeguato ed avvitata saldamente alla carpenteria della macchina. Sui carter sono attaccate delle targhe indicanti il divieto di accesso alla zona in condizioni di macchina elettricamente alimentata.
-
Riparo fisso su morsa pneumatica: disposto a protezione del pericolo di cesoiamento per il movimento alternativo del cilindro. (Fig.4-8).
Per operazioni di manutenzione che richiedono la rimozione dei ripari fissi, è fatto obbligo di isolare la macchina dalla rete di alimentazione elettrica aprendo l’interruttore generale posto sulla parte frontale della macchina. Al termine dell’intervento, rimettere i ripari nelle condizioni operative originali onde evitare pericoli di infortunio.
-
Armadio elettrico: l’interruttore generale di sezionamento della macchina dalla linea elettrica (Fig. 4-6) toglie la tensione a tutto il macchinario. Sul quadro elettrico, sono riportate le targhe indicanti i rischi connessi alla presenza di tensione elettrica. (Fig.4-3).
-
Circuiti dei vari fluidi: i circuiti sono stati realizzati con tubazioni idonee alla pressione di esercizio. I circuiti di comando, in accordo con le norme, sono stati realizzati in bassa tensione (24 Vcc). (Fig.4-1)
Rischi residui
La semplice avvertenza sull’esistenza di un rischio residuo, non è accettabile nel caso in cui tale rischio sia eliminabile con dispositivi di sicurezza. L’elenco dei rischi residui, può essere associato ad utilizzi scorretti ed operazioni non condotte secondo quanto trascritto nel presente manuale:
-
Relativi a operazioni di manutenzione sul circuito idraulico, pneumatico e altri circuiti dei gruppi operatori montati sulla macchina. Rischio di possibile proiezione di fluidi se non vengono scaricati i circuiti prima di operare.
-
Relativi a operazioni di regolazione dei relativi dispositivi facenti parte dei gruppi operatori se non vengono adottate le misure di sicurezza per operare all’interno del vano della macchina.
-
Relativi alle operazioni di manutenzione sull’impianto elettrico se non si isola la macchina correttamente. Rischio di contatto con parti in tensione qualora si operi senza avere isolato la macchina dalla linea elettrica di alimentazione. Apposite targhe riportate sul quadro elettrico, richiamano il rischio ed il divieto di accesso su apparecchiature in tensione.
Targhe di sicurezza
Sulla macchina, sono affisse targhette per avvertire l’operatore del pericolo potenziale che esiste in quella zona.
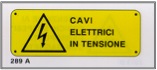
Dimensioni
La macchina non è molto ingombrante e non presenta grosse sagomature geometriche che necessitano di particolari posizionamenti.
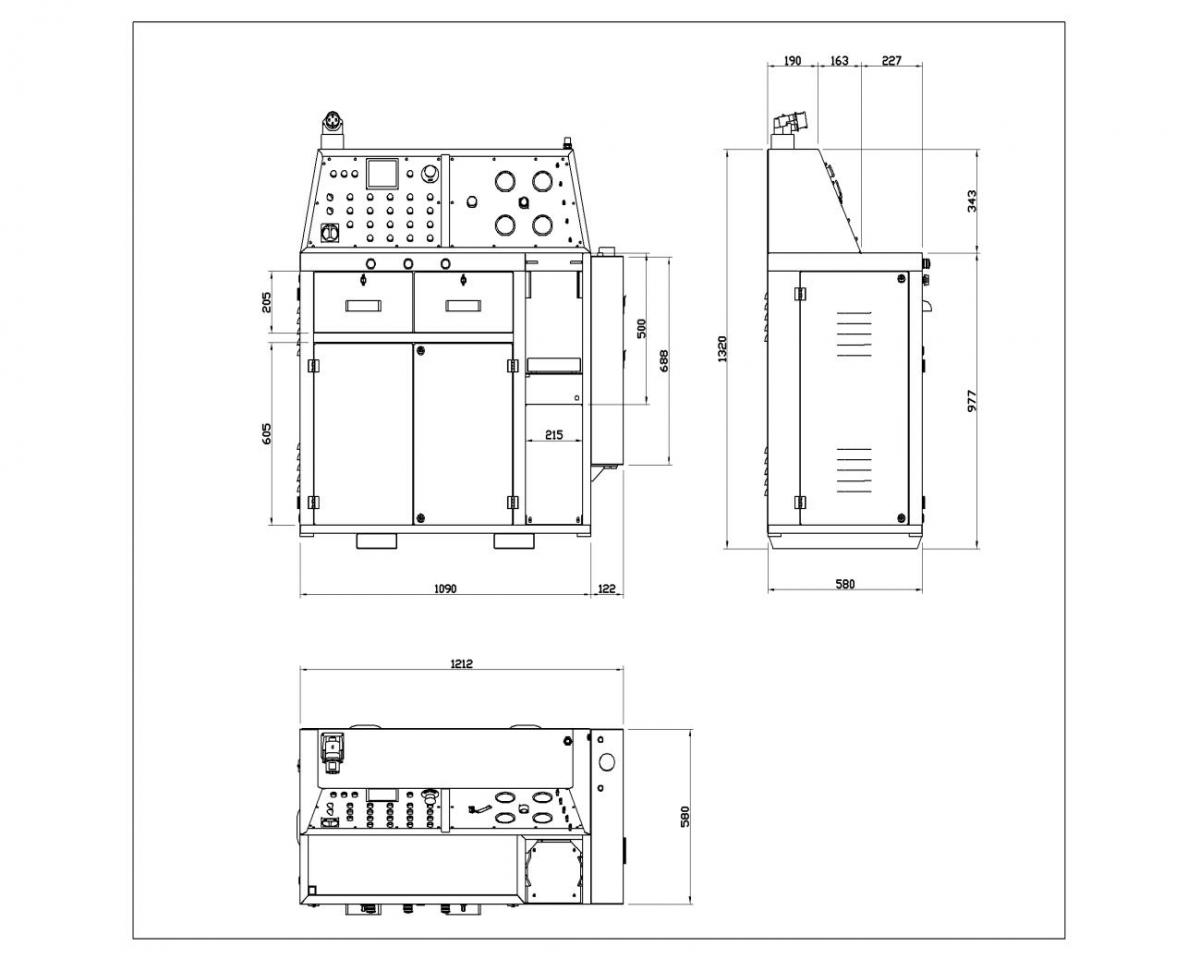
Fig.5
Area di ingombro
La macchina va installata in modo tale che intorno sia disponibile un’area sufficiente da permettere
agevolmente le operazioni di uso e di movimentazione del materiale da lavorare.
Nella figura sono riportati gli spazi minimi necessari per le normali operazioni di uso e manutenzione.
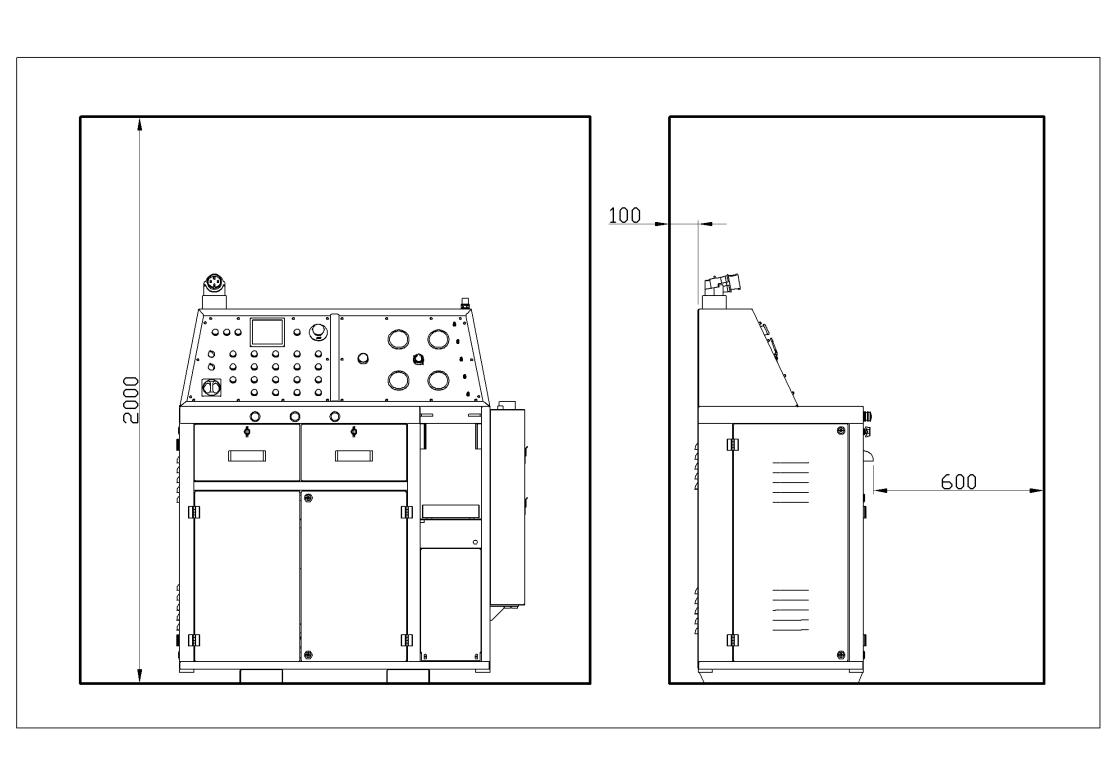
PAG. SUCCESSIVA. >>>